Hi all,
I have been playing around with the frequency simulation, doing astudy on a part using different approaches and meshes. What I amdoing a study on is a hollow core metal door with a uniform wallthickness of .125". I have approached it in the following ways:
1. As a solid body with a very fine, standard mesh.
2. As a solid body with a very fine curvature based mesh.
3. As a 3D surface feature, with an assigned shell thickness of.125" and specified as "thin" with a very fine standard shell mesh.
4. As a 3D surface feature, with an assigned shell thickness of.125" and specified as "thin" with a very fine curvature basedshell mesh.
5. As a 3D surface feature, with an assigned shell thickness of.125" and specified as "thick" with a very fine standard shellmesh.
6. As a 3D surface feature, with an assigned shell thickness of.125" and specified as "thick" with a very fine curvature basedshell mesh.
Simulating these ways gives significantly different results. Thefrequencies at a certain mode are varying by almost 900 hertzbetween the highest and lowest frequency from the six results. Bothof the solid body simulations with either mesh give results thatare similar to each other but on the higher end and the shell meshresults are similar to each other but on the lower end.
So I have some questions. When doing a frequency analysis, why dothe frequencies vary so much between shell and solid meshes? Whatis the real difference between specifying the surface body aseither thin or thick and when would one be used over the other?Which of the methods I did would be the most accurate method offinding the frequencies (I honestly have no idea what they would befor this door)?
*edit* forgot to mention that I am applying no forces or restraintsto the body
SolidworksSimulation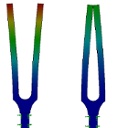
I have been playing around with the frequency simulation, doing astudy on a part using different approaches and meshes. What I amdoing a study on is a hollow core metal door with a uniform wallthickness of .125". I have approached it in the following ways:
1. As a solid body with a very fine, standard mesh.
2. As a solid body with a very fine curvature based mesh.
3. As a 3D surface feature, with an assigned shell thickness of.125" and specified as "thin" with a very fine standard shell mesh.
4. As a 3D surface feature, with an assigned shell thickness of.125" and specified as "thin" with a very fine curvature basedshell mesh.
5. As a 3D surface feature, with an assigned shell thickness of.125" and specified as "thick" with a very fine standard shellmesh.
6. As a 3D surface feature, with an assigned shell thickness of.125" and specified as "thick" with a very fine curvature basedshell mesh.
Simulating these ways gives significantly different results. Thefrequencies at a certain mode are varying by almost 900 hertzbetween the highest and lowest frequency from the six results. Bothof the solid body simulations with either mesh give results thatare similar to each other but on the higher end and the shell meshresults are similar to each other but on the lower end.
So I have some questions. When doing a frequency analysis, why dothe frequencies vary so much between shell and solid meshes? Whatis the real difference between specifying the surface body aseither thin or thick and when would one be used over the other?Which of the methods I did would be the most accurate method offinding the frequencies (I honestly have no idea what they would befor this door)?
*edit* forgot to mention that I am applying no forces or restraintsto the body
SolidworksSimulation